Moving away from disparate, spreadsheet-based budgeting and forecasting processes, Toyota Motor Europe (TME) is using the Board Enterprise Planning Platform to create a standardized approach across all 40 companies within the Group. Financial reporting and variance analysis, P&L generation, five-year CAPEX planning, and scenario modeling are to be conducted in one, unified solution with greater control, including the possibility to choose among different methodologies, such as zero-based budgeting or driver-based planning.

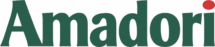
Consumer Packaged Goods
Transformation of Demand Planning Processes at the Amadori Group