Manufacturing and Distribution Planning
At CRGroup, we understand the unique challenges faced in manufacturing & distribution. As a premier Board Partner with over 30 years of industry experience, we help companies build a complete and effective corporate performance management process in Board in order to understand key business drivers and achieve:
- Full visibility of performance across inventory, supply chain, quality control, and fulfillment
- Alignment of supply chain and production plans with sales and demand forecasts
- Real-time reporting and insights for agile leadership and management
- One holistic view of company performance from high-level strategic KPIs down to SKUs
Streamline Planning & Analysis Across Your Entire Company
We can help aggregate operational data from multiple regions, business lines, cost centers, and plants in order to link them to your company’s financial and business goals. Using the tools available in Board, CRGroup’s team of experts can help you:
- Produce variable revenue plans and forecasts
- Forecast costs for materials, labor and overhead
- Calculate and analyze production costs
- Streamline consolidation and reporting
- Conduct product and customer profitability analysis
- Use drivers to streamline planning
- Assess resource availability
Understand the Impacts of Every Area of Operation
From planning, simulation, forecasting, and analysis, we help companies implemented and run one unified data environment, to achieve a better understanding of the impact of operational decisions on working capital, cash, revenue, and profitability across multiple levels.
Get started today! Book your free consultation to learn how we can help transform your company with Board.
Want to see this solution in action?
Complete the form and our specialists will be in touch.
Other solutions
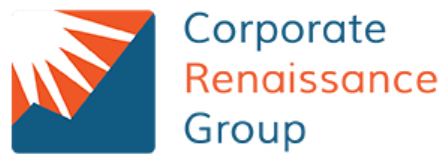
